Superwood, developed by InventWood, offers a strength-to-weight ratio nearly ten times that of steel while weighing just one-sixth as much. You’ll find this engineered wood product boasts extreme weather resistance, fire protection, and pest resistance. The manufacturing process removes lignin through chemical treatment and compresses the wood to align cellulose nanofibers. With commercial production starting in late 2025, this renewable alternative could transform construction and manufacturing industries worldwide.
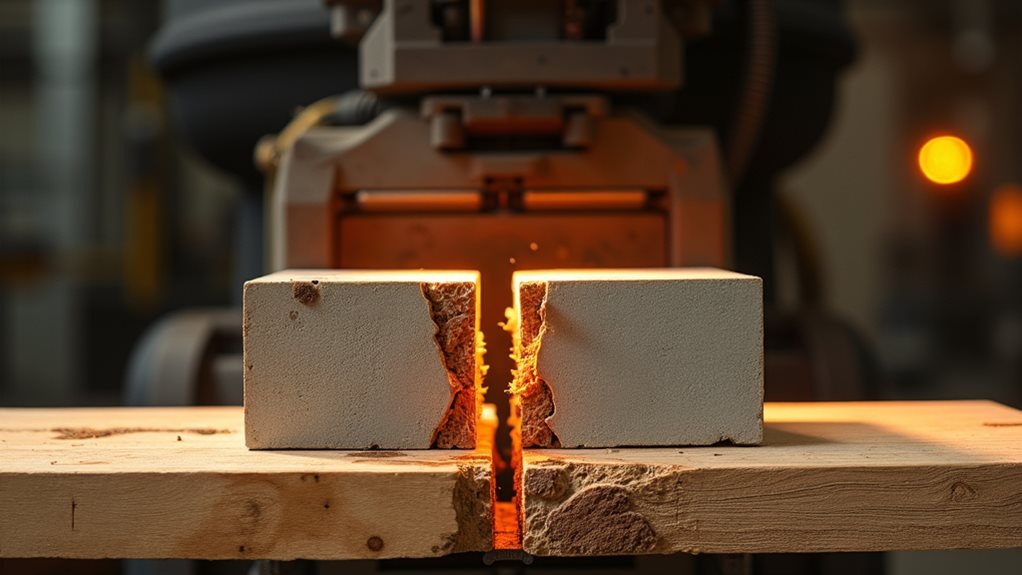
A revolutionary new material called superwood is challenging steel‘s dominance in construction and manufacturing. This engineered wood product demonstrates strength up to 12 times greater than natural wood while maintaining approximately one-sixth the weight of steel.
You’ll find that superwood offers an impressive strength-to-weight ratio nearly ten times that of steel. This makes it remarkably efficient for structural applications where weight matters, such as in vehicles and aircraft.
The manufacturing process involves boiling wood in a mixture of sodium hydroxide and sodium sulfite. This chemical treatment partially removes lignin and hemicellulose without creating considerable pollution concerns.
Transforming ordinary lumber into superwood requires a specialized chemical bath that strips away natural components while maintaining environmental standards.
The wood then undergoes heat compression, collapsing cell walls and densely aligning cellulose nanofibers. The process includes mild heat treatment at approximately 150°F to optimize the compression results. This two-day process results in wood that’s about 20% thinner but substantially stronger than its untreated counterpart.
Developed by InventWood, a University of Maryland spin-off, superwood represents a significant advancement in sustainable materials science.
Ten times more energy is required to fracture superwood compared to natural wood, demonstrating its exceptional durability.
Unlike conventional building materials, superwood retains wood’s natural qualities like warmth and texture while being engineered to withstand extreme weather and high humidity. It boasts a Class A fire rating and strong resistance to rot and pests.
You can bend and mold superwood, creating versatility that traditional wood products don’t offer. This adaptability makes it suitable for numerous applications typically dominated by steel or titanium alloys.
The material represents a renewable alternative to carbon-intensive metals. Its production is potentially cheaper and requires less energy than metal manufacturing, with transportation savings due to its lighter weight.
Superwood’s potential extends to buildings, vehicles, airplanes, and other structural applications. The first mass production facility in Frederick, Maryland, is expected to begin shipments in late 2025, with over $50 million already raised for commercial scaling.
While outperforming steel in strength-to-weight comparisons, superwood remains less expensive than carbon fiber alternatives. Its combination of strength, sustainability, and workability positions it as a formidable challenger to traditional metals in construction and manufacturing.
Frequently Asked Questions
Is Superwood Environmentally Friendly to Produce?
Yes, you’ll find Superwood is highly environmentally friendly to produce.
It creates 90% lower carbon emissions compared to steel production and uses ordinary wood from sustainable sources.
The manufacturing process utilizes common industrial compounds like lye and sodium sulfite.
Superwood carries FSC and PEFC certifications, guaranteeing responsible sourcing practices.
The material’s local transportation (typically within 200 km) further minimizes its environmental footprint, making it a genuinely sustainable alternative to metal.
What Is the Cost Comparison Between Superwood and Steel?
You’ll find limited cost data comparing Superwood and steel directly.
Based on the background information, steel typically costs more upfront than wood materials, with steel framing about 5% more expensive than wood trusses.
Since Superwood is a relatively new innovation, its production costs aren’t widely documented.
The economics likely depend on manufacturing scale and regional availability of raw materials, though its reported superior strength might justify premium pricing compared to regular wood.
How Does Superwood Perform in Extreme Temperatures?
Superwood maintains its structural integrity in extreme temperatures better than natural wood.
You’ll find it offers good thermal stability, though specific temperature thresholds aren’t well-documented.
Its engineered fire resistance is particularly valuable in high-temperature environments. The material can withstand harsh conditions without considerable deterioration.
While extreme heat might affect moisture-related issues in traditional wood, Superwood’s water-repellent properties help mitigate this concern, making it suitable for varying temperature applications.
Can Superwood Replace Steel in All Construction Applications?
No, superwood can’t fully replace steel in all construction applications yet.
You’ll find it has limitations despite its impressive strength-to-weight ratio.
Water vulnerability remains a notable challenge, as increased moisture reduces its strength.
Scalability issues also exist in manufacturing processes.
Additionally, superwood needs more extensive testing and established construction standards.
It’s most promising for architectural façades and specific structural elements, but complete steel replacement would require considerable changes in construction practices and further technological advancements.
What Is Superwood’s Expected Lifespan Compared to Traditional Materials?
Superwood’s expected lifespan considerably exceeds traditional wood thanks to its improved resistance to fire, water, and rot.
You’ll find that while traditional wood can last decades to centuries depending on species and conditions, superwood’s molecular transformation creates exceptional durability without requiring preservative treatments.
Compared to steel, superwood doesn’t corrode and maintains its structural integrity longer in harsh environments.
However, exact lifespan metrics aren’t yet established as this innovative material continues undergoing long-term performance testing.